Table of Contents
Intro
As the holiday season approaches, the demand for professional Christmas light installation services skyrockets. For those in the industry, ensuring efficient and organized operations is crucial to delivering exceptional results for clients. In this blog, we’ll delve into the meticulous process of prepping and loading a truck for a day of Christmas light installation, as shared by the experts at Christmas Light Contractors USA.
Bins
To maintain a seamless workflow, the team at Christmas Light Contractors USA has developed a systematic approach to organizing their equipment and supplies. They utilize a series of labeled bins, each containing specific items needed for a successful installation.
The first bin is dedicated to the essential components – the C9 minion bulbs. These pre-bulbed, warm-white LED lights are the backbone of their installations, with each trash can holding up to 500 feet of the 33-gram, 32-gallon, pro-grade, ever-built variety. The locking lids allow for easy stacking and transportation.
The second bin houses the C7 bulbs, which are used for various applications, such as wreaths and trees. This bin also includes the team’s blinker bulbs, a crucial element for adding dynamic visual interest to the displays.
The third bin is the tools bin, containing a comprehensive collection of essential equipment. This includes vinyl-coated wire for wreaths, landscape staples for securing wires, a kilowatt meter, snips, hog-nose pliers, a backup hook for their extension pole, and a variety of replacement sockets and inline female connectors.
The fourth bin is dedicated to the team’s clip collection. This bin holds an extra 300 enclosed clips, as well as ground stakes, track clips, magnetic clips, and ridge clips – ensuring they have a diverse range of fastening solutions for any installation scenario.
The final bin is the power wire bin, which contains a thousand feet of various wire colors, along with 10 timers and extra extension cords. This bin allows the team to easily access and replenish their power supply needs throughout the day.
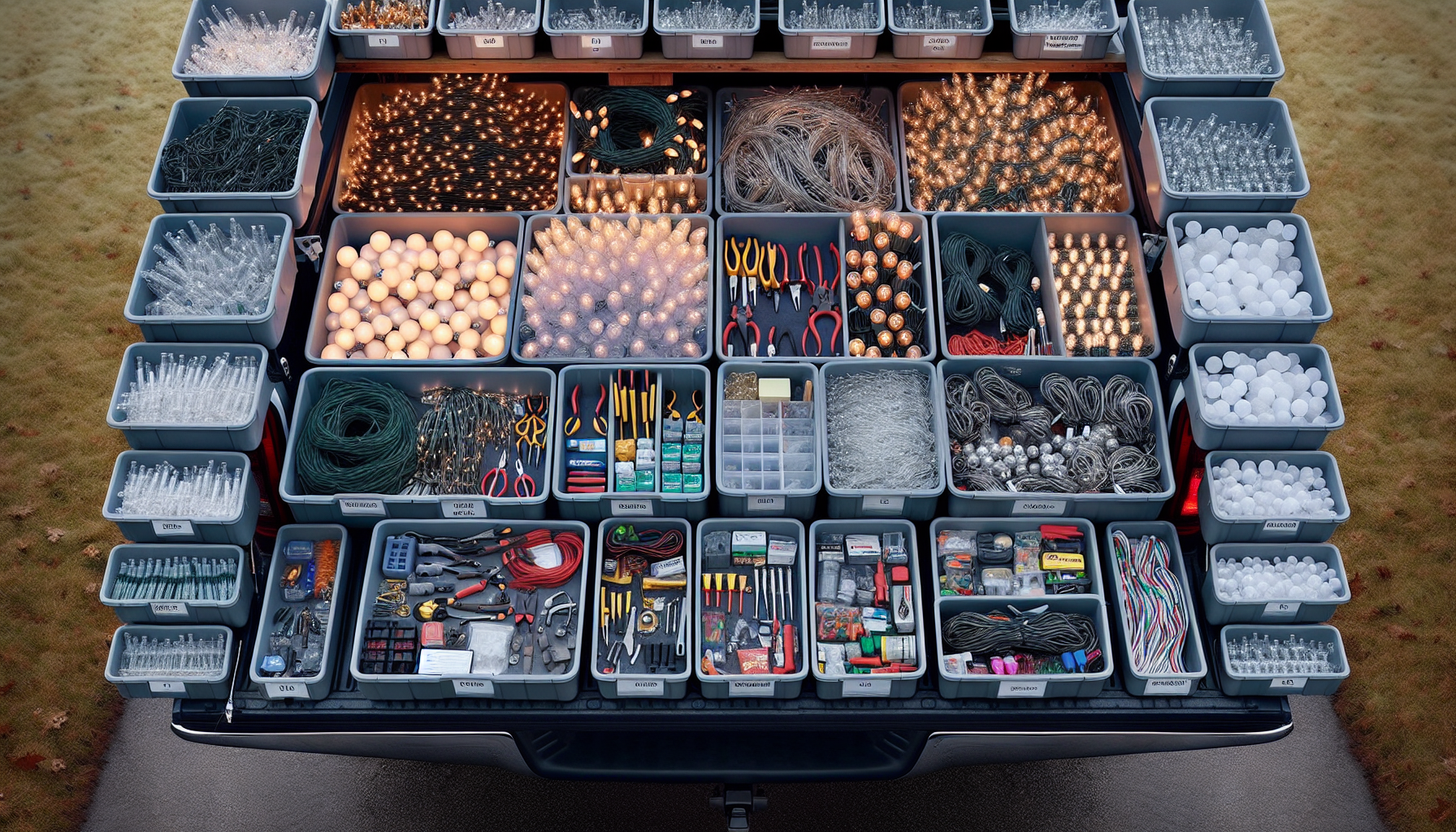
Minion
At the heart of the Christmas Light Contractors USA’s lighting installations are the pre-bulbed mini lights. These professional-grade stringers come pre-bulbed and tagged, eliminating the time-consuming task of individually bulbing each string. Depending on the number of houses they’re servicing for the day, the team will grab two, three, or four crates of these 50-foot stringers, each containing 40 individual strands.
The team also has a collection of C7 bulb stringers, which they use for their tree installations. The number of stringers they’ll need for each tree varies, but they typically have a few bins of these on hand, with 15 stringers per bin.
Tools
In addition to the specialized bins, the team also maintains a collection of client-specific lighting bins. These bins contain the lights that have been reinstalled from previous years, as well as any special requests or new installations that are ready to go. By having these bins readily available, the team can quickly grab the necessary equipment for each job, ensuring a seamless and efficient installation process.
The organization doesn’t stop there. The team has a designated area inside their facility where all the prepared bins, trash cans, and client-specific lighting bins are stacked and ready to go. This centralized staging area allows the team members to simply grab the bins they need and head out to their assigned trucks, without the need for extensive searching or preparation.
At the end of each day, the team ensures that everything is removed from the trucks and properly reorganized and restocked. This end-of-day routine guarantees that the trucks are ready to go for the next day’s installations, minimizing downtime and maximizing productivity.
Outro
The meticulous approach employed by the team at Christmas Light Contractors USA is a testament to their commitment to excellence and efficiency. By meticulously organizing their equipment, streamlining their processes, and maintaining a well-stocked inventory, they are able to deliver exceptional Christmas light installations with ease.
Whether you’re a professional in the industry or a homeowner looking to enhance your holiday display, the insights shared in this blog can serve as a valuable guide for optimizing your own Christmas light installation efforts. By adopting a similar level of organization and attention to detail, you can ensure a seamless and stress-free holiday season, both for yourself and your clients.
FAQ
- What type of bulbs do you use for your Christmas light installations? We primarily use C9 minion bulbs, which are pre-bulbed, warm-white LED lights. We also utilize C7 bulbs for various applications, such as wreaths and trees.
- How do you organize your equipment and supplies? We have a comprehensive system of labeled bins, each containing specific items needed for a successful installation. This includes bins for bulbs, tools, clips, power wires, and client-specific lighting.
- How do you ensure your trucks are ready for each day’s work? At the end of each day, we remove everything from the trucks and properly reorganize and restock the bins. This end-of-day routine guarantees that the trucks are fully prepared for the next day’s installations.
- What type of pre-bulbed mini lights do you use? We use professional-grade, pre-bulbed mini lights that come in 50-foot stringers, with 40 individual strands per crate. This eliminates the need for individually bulbing each string, saving us time and effort.
- How do you handle client-specific lighting requests? We maintain a collection of client-specific lighting bins, which contain the lights that have been reinstalled from previous years, as well as any special requests or new installations that are ready to go. This allows us to quickly grab the necessary equipment for each job.